How the servo mechanism works in industrial automation?
Servo-mechanism is an element that is inextricably linked with the concept of industrial automation, wherever precision and repeatability must be maintained. The most common application of servo mechanisms in industrial automation is controlling the position of machine elements (e.g. head), adjusting the rotational speed of rotors, controlling stresses and pressure force, or maintaining a constant torque. But let’s go back to the basics and define the issues related to the servo.
What the servo-mechanism is?
A servo, also sometimes called a servo drive, servo or servo motor, is a type of device that makes rotational movement to drive components of a machine.
Properties of servo-mechanisms
Servomechanisms can have various dimensions and parameters tailored to the needs of a given application.
Generally speaking, in the production of electronics, a servo drive is a basic control module for the automation of industrial devices or machines in a closed system. The electronic components contained in the servo allow the conversion of analog or digital control signals into precise movement of the end elements. The servo mechanism enables precise adjustment of the parameters of acceleration, speed and the force of sliding end elements on the basis of feedback. The operation of the servomechanism based on the feedback principle is carried out by an encoder with a potentiometer.
Servomechanisms have several important features:
- Possibility to move large and heavy components
- Capable of working with very high positive and negative accelerations
- Working at high speeds
- Precise control capability and position feedback
- Low sensitivity to working environment conditions
Construction of the servo
Servomechanisms consist of 5 key components. These are:
- Engine
- Driver with amplifier
- Encoder
- Gear
- Mechanical housing
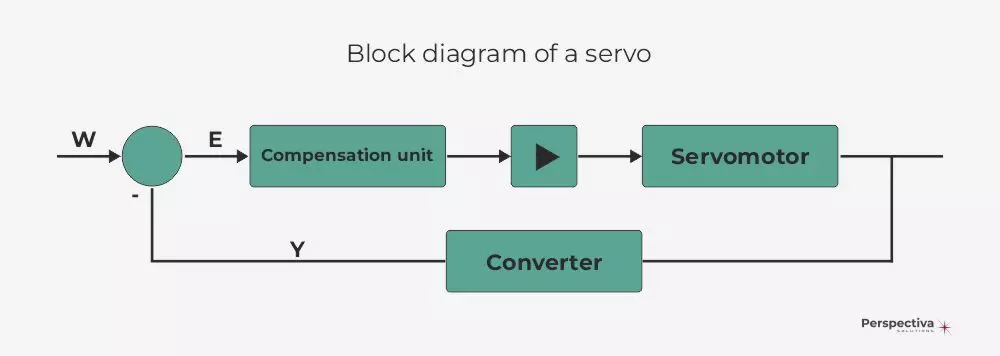
Servo drive / servo motor - the motor in the servo
Silnik w serwomechanizmie jest jednym z jego podstawowych elementów, który umożliwia kontrolowanie dokładnej pozycji elementu obrotowego w postaci wału silnika, jego przyśpieszenia i prędkości obrotowej. Serwomechanizm napędzany jest silnikiem elektrycznym stałego prądu (DC) lub prądu przemiennego (AC), który może być używany do precyzyjnego sterowania ruchem. Serwo używane są często w aplikacjach, w których trzeba zachować precyzję i/lub dużą siłę.
Serwomotor kontrolowany jest poprzez sterownik. Pomaga on w utrzymaniu precyzyjnego położenia obracającego się elementu, dzięki wykonywaniu precyzyjnych i dokładnych ruchów elementów końcowych. Silnik generuje siłę, która jest przenoszona na obracające się elementy poprzez przekładnię.
Driver with amplifier - How to control the servo?
A controller is required to control the servo, which helps to maintain the precise position of the rotating element and also stores all the parameters of the servo amplifiers. Such an approach allows the servo to make precise and precise movements of the end element. The servo is controlled electronically, not mechanically. This makes the controlling system very precise and accurate.
What is the servo encoder for?
The encoder is an element that is usually physically located in the servo motor. It is primarily used to control the position of the motor, measure the speed and the direction of rotation. Its operation allows you to maintain precise engine control.
There are two types of encoders: relative and absolute. Relative encoders measure the displacement from the zero position, which is most often set after power-up or with the software. Absolute encoders, on the other hand, do not need a voltage sustained to determine their position. Their zero position is predetermined at the production stage and is always exactly in the same place.
The servomechanism with the encoder is a mechanism that enables precise control of mechanical movements. This mechanism is used in many areas, such as industrial automation, aviation and electronics. The servo consists of a motor, gear, and encoder.
The servo motor drives the gearbox, which in turn controls the workpiece. The encoder is used to measure the speed and direction of rotation of the motor, as well as to monitor the position of the working element. In a servo, an encoder is a type of motion control sensor that is responsible for providing feedback to the control system. It works by converting the rotational or linear motion of machine parts into an electrical signal. This signal is read, for example, by means of a counter or the PLC of the machine in the control system and accurately determines the position of the various machine elements, the angle, the number of revolutions of the motor shaft, the rotational speed, its direction and position. Thanks to such an approach, it is possible to maintain precise motor control in the servo.
Servo transmission
The gearbox is the mechanism that transfers the energy generated by the engine to the final working element. During the transfer of energy to the working element, it is possible to change its torque and speed at the same time. The idea is to transfer electricity from the magnet coil to the shaft. It is also possible to change the direction of rotation by turning to the right or left.
An important point to mention is the change from rotary to linear motion and vice versa. Gears in servo motors often also receive the function of transmitting energy over a distance, and this is done by using, for example, a V-belt or chain. In the case of servomechanisms, the most commonly used mechanical gears, which are characterized by high efficiency and are highly precise.
There is a wide variety of mechanical gears in the industry that are often used in servo motors.
The most popular mechanical transmissions are:
- gear of gears,
- friction gear,
- cable transmission,
- belt transmission,
- v-belt transmission,
- chain transmission,
- bearing gear,
- helical gear,
- planetary gear.
There are also other types of gears on the market, they are classified according to the physical phenomena used, which are:
- hydraulic transmissions,
- pneumatic gears,
- electric gears.
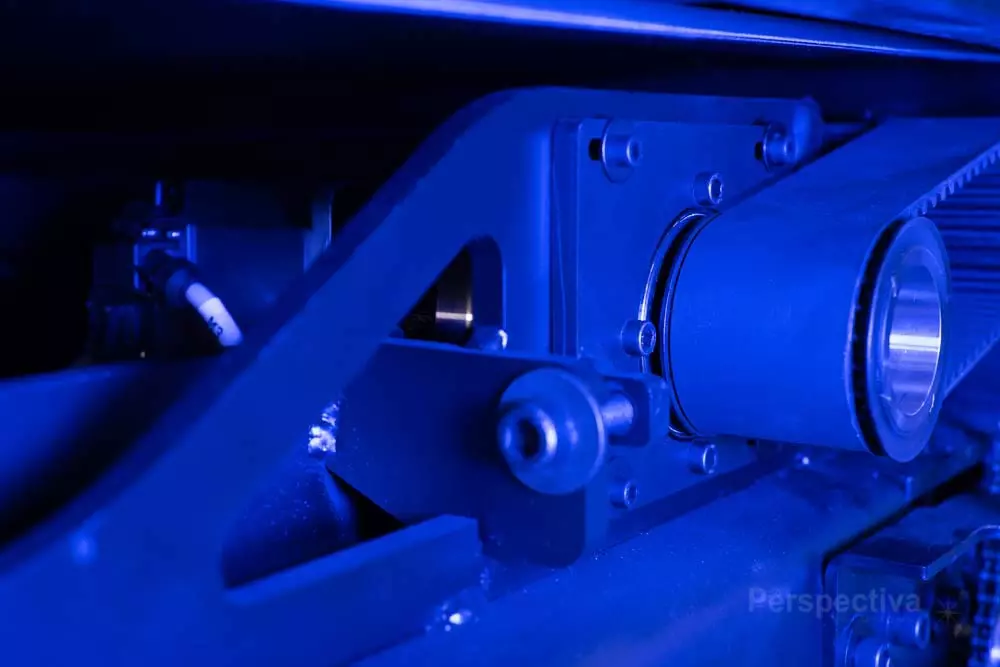
Servo mechanical housing
The mechanical enclosure of the servomotors is responsible for the two main functions:
- protects the engine against damage in the event of external mechanical and environmental factors,
- allows the engine to be mounted in a device or machine.
The housings of servo drives are most often made of metals, mainly aluminum alloys.
How does the servo-mechanism work?
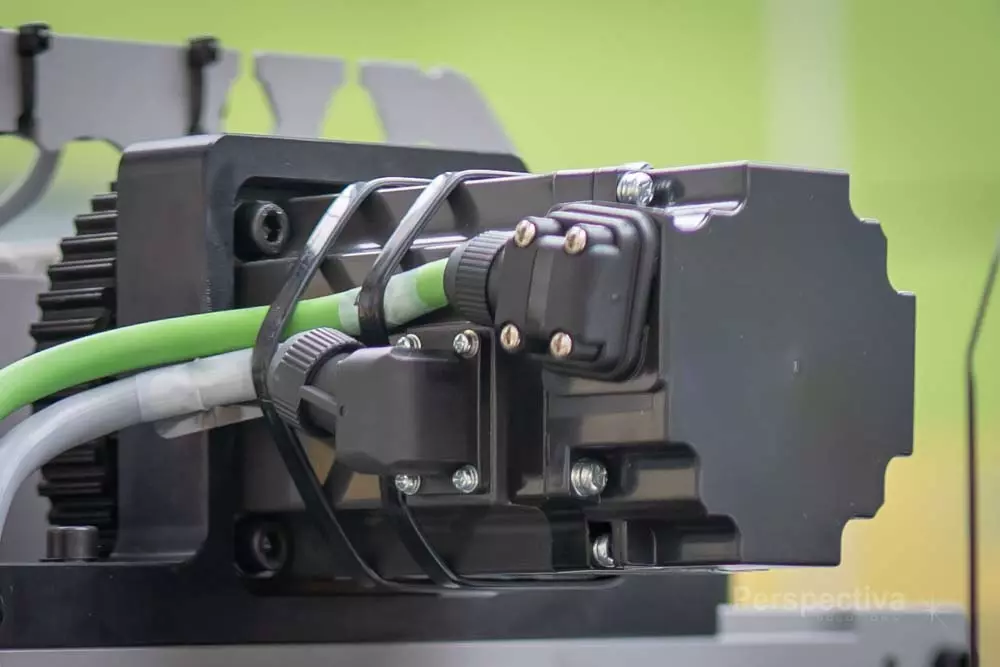
The servo motor is responsible for rotating the machine shafts. In other words, it converts the electrical energy supplied to it into mechanical energy of rotational motion. The mechanical energy of the engine is transferred not directly, but by means of gears that adjust the rotational speed of the shafts to the desired level. They also regulate the torque. The operation of the engine is controlled by a controller which receives information from another device (e.g. PLC controller). The controller based on that information will generate appropriate electrical signals to control the engine. Another very important component is an encoder. It is positioned in the feedback loop and it provides the controller with the information about the current position of the motor. This enables precise control of the rotational movement.
Different types of servo drives can have quite a wide range of possibilities and designs. Nevertheless, with some simplification, we can assume that they contain all the above components.
The main parameters of servos are:
- working time when overload,
- torque and rotational speed,
- resolution,
- frequency response,
- interfaces,
- dimensions,
- network options,
- torque to inertia ratio.
Different types of servo drives can have quite a wide range of options and designs. Nevertheless, with some simplification, we can assume that they contain all the above components.
Feedback loop in servo
The feedback loop provides information on the current position of the work piece. This in turn allows the controller to precisely control the motor to achieve the desired servo position. The servo feedback plays a key role in the precision of the servo operation. The feedback output is some data (e.g., position, velocity, acceleration, displacement). We distinguish between positive and negative feedback.
How does feedback work in a servo?
The controller uses a feedback loop and an encoder to read the current position of the motor. It then checks the desired set value for the position that the motor should have. The driver calculates the difference between these values. If it is equal to zero, it means that the motor has reached the required position. If, on the other hand, it is different from zero, then the controller calculates the correction (offset) and drives the motor to make the move until reaching the zero value for the difference between the setting and the actual read position.
The servo feedback is achieved by direct control of the motor’s electromagnetic field. This process is often called “phase control”. In the case of phase control, electromagnetic field control is performed to achieve the desired speed and torque. Phase control is often used, for example, in staircase servo drives, which must be very accurate.
Computer control of servo drives is often performed with a control card. Correct phase adjustment requires that the control card be able to read information from the encoder and adjust the electromagnetic field to the desired setting. For some applications, however, it may also be necessary to determine whether the shaft is turned to the left or to the right.
Applications of servo-mechanisms
Servomechanisms are used in many industries. They are critical components for the correct and efficient operation of the machines. The servo is used in particular in various types of industrial machines, automation, robotics and modeling. The main task of the servo in machines is to determine the position of the motor shaft, its synchronization, as well as the elimination of control errors, e.g. displacement error.
Servomechanisms can also be used when it is necessary to precisely control a rotating element. Often the servos are used in industry to ensure accurate and precise production. They can also be used to control items that need to be moved in a specific order. As a result, servos are often used in production lines where they are used to drive the production line or other machine elements.
Servomechanisms can have various dimensions and parameters adapted to the needs of a given application. They may also have additional accessories (e.g. ski lifts, branching cables, minicomputers). A specific feature of servomechanisms is their integrating nature of the actuator with dynamics that do not hinder regulation, but in turn brings non-linearity in their characteristics. Due to this, servos require the use of proportional regulators with high gain or three pole amplifiers.
Servomechanisms are used in applications such as:
- levers and switches,
- valves and dampers,
- blinds and shutters,
- lever mechanisms,
- hand tools,
- industrial automation,
- industrial robotics,
- aircraft,
- agricultural machinery,
- CNC machines,
- cars,
- model making.
How to choose the servo to your application?
The correct operation of many advanced production machines depends on the appropriate selection of the servo for the machine, as well as the optimal operation of each of its complex elements.
When choosing the right servo used in industrial automation, several factors should be taken into account:
- type of servo (analog, digital),
- size (e.g. micro, standard) – depending on the model, they differ in size and weight,
- servo force – determines the torque value generated on the servo lever,
- speed of its operation – determines the speed at which the servo rotates the unloaded dragline,
- type of gear (e.g. metal, carbon) – one of the elements generating the force of the servo,
- application specificity – individual selection of a servo for a given device.
Design of signal electrical harnesses used in servo-mechanisms
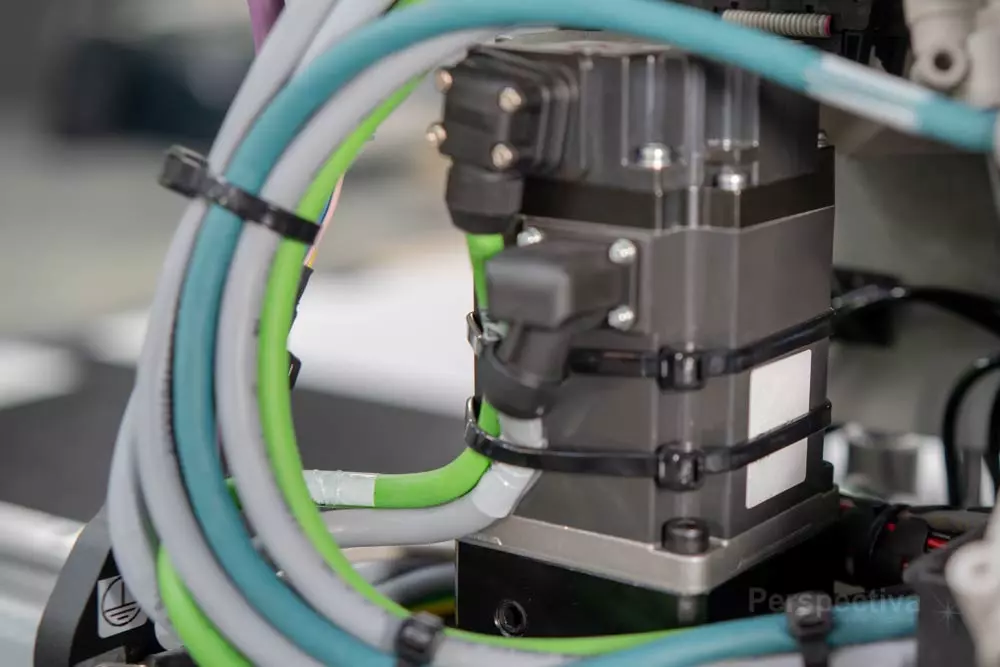
The correct selection of a wiring harness for a servo-driven machine is a more complicated process than you might think. The connection of cables with the servo is a key element for the proper operation of the machine and for the efficient connection system used in machines of various types. However, it is often underestimated. In the context of cable harnesses used in servo drives, it is crucial to realize that the working environment of these devices is usually areas with a very high level of so-called electromagnetic smog. There are many devices around the servo that generate noise in the form of electromagnetic waves. Therefore, the harnesses used in servo drives must be designed in such a way that interference does not affect the operation of the servo, for example, the reading values of the encoder.
The harnesses used in servos must meet several key requirements:
- must effectively shield (block) electromagnetic waves thanks to cables with an appropriate degree of filling factor of the the side surface with shielding material,
- have high mechanical resistance,
- be able to perform a specified number of bending cycles in the case of placing the cable in the cable chain,
- demonstrate resistance to chemicals that may be present in the operating environment of a servo-driven machine.
To conclude, it is important that the harnesses working with servo motors are developed and made with the use of specialist knowledge and due care. Otherwise, the servo may just not work.
Check out our servo related services
Note: The use of graphics from the article “How the servo mechanism works in industrial automation?” is allowed as long as the source (link to the page) is mentioned.
Suggested articles related to the topic of servos
- Own production vs. outsourcing – when to commission contract production
- Production outsourcing – The optimal solution for scaling company
- How the electric harness is produced?
- Prototyping of machine wiring
- Bespoke cable harness: designing an electric harnesses for the customer needs
- How to choose an electrical harness correctly?
Lino
16 October 2022Thanks for a good article that easily shows the issues of servo mechanizm. You can also add more diagrams and sections of servos. In servo applications can also be supplemented with eg. packaging machines, labellers, winding machines.
admin
20 October 2022Thank you for your comment. Of course, we will try to supplement the article with additional servo graphics in the near future.
Hulodeg
18 November 2022Hello. Great blog about what is a servo motor and how it works amd how control it. Especially in define servomechanism and industrial servo motor subject. I am also associated with industrial automation so i wonder what servo motors you have used most often so far?