Jak powstają wiązki elektryczne?
Wiązki elektryczne stanowią kluczowy element współczesnej technologii, stanowiąc skomplikowaną sieć połączeń elektrycznych w różnorodnych urządzeniach i systemach. W artykule „Jak powstają wiązki elektryczne?” przyjrzymy się krok po kroku procesowi tworzenia w naszej firmie niezawodnych i bezpiecznych wiązek kablowych. Dowiedz się, jakie materiały są wykorzystywane oraz dlaczego precyzja w tworzeniu wiązek kablowych ma kluczowe znaczenie dla efektywnej pracy urządzeń elektronicznych.
Chcesz się dowiedzieć, na czym polega produkcja wiązek elektrycznych? Potrzebujesz szybkiej wiedzy w temacie jak zrobić wiązkę elektryczną? Oto pełne podsumowanie, na czym polega powstawanie wiązek elektrycznych, czyli proces budowania wiązki kablowej w kilku kluczowych etapach.
Z tego artykułu dowiesz się:
- Co to są wiązki elektryczne?
- Projektowanie wiązek elektrycznych
- Co to jest BOM materiałowy?
- Cięcie i odizolowywanie przewodów wiązek kablowych
- Etykietowanie i znakowanie wiązki elektrycznej
- Zaciskanie lub lutowanie terminali
- Taśmowanie lub wiązanie opaskami wiązki elektrycznej
- Międzyoperacyjna kontrola jakości produkcji
- Montaż wiązek kablowych
- Końcowa kontrola jakości gotowej wiązki elektrycznej
- Przygotowanie wiązek elektrycznych do transportu
Popularne typy wiązek kablowych
W ofercie Perspectiva Solutions można znaleźć dedykowane wiązki kablowe pod zamówienie, a także popularne typy wiązek elektrycznych, szeroko stosowane w różnych gałęziach przemysłu. Standardowe wiązki kablowe jesteśmy w stanie wyprodukować i dostarczyć w ekspresowym tempie.
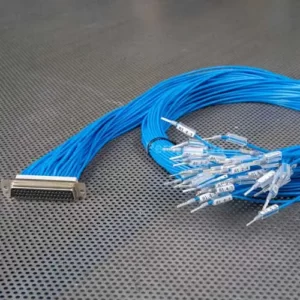
Wiązka elektryczna synchronizacji sygnałów
To przykład realizacji produkcji wiązki sygnałowej łączącej obudowę urządzenia z aparatami, które stosują zaciski uniwersalne. Np.: na szynie DIN.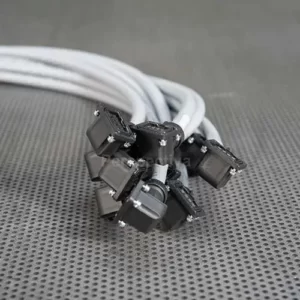
Wiązka elektryczna zasilająca silnik enkoderowy
Wiązka typowo stosowana w produkcji zasilania napędów enkoderowych w robotach przemysłowych takich firm jak Mitsubishi, Fanuc, Yaskawa, ABB, itd.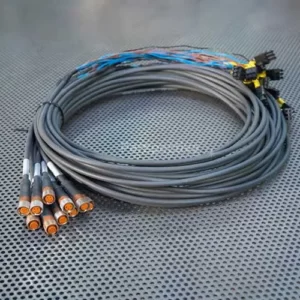
Wiązka kablowa czujnika
Produkcja wiązek kablowych z czujnikiem to przykład realizacji wiązki ze standardem M, który pozwala na połączenie z czujnikami stosowanymi w liniach produkcyjnych.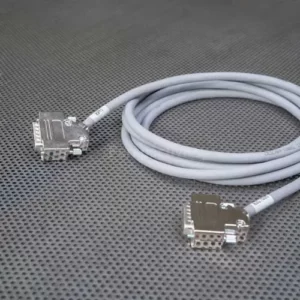
Wiązka kablowa CAN
Typowa wiązka sygnałowa stosująca powszechnie używany standard złączy DB Cannon. Produkcja wiązek kablowych z szyną CAN często jest stosowana dla sektora motoryzacji.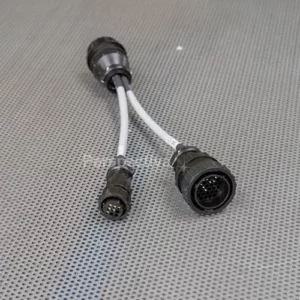
Wiązka elektryczna ze złączami AMP
Wiązki elektryczne tego typu produkuje się montując złącza AMP i inne. Stosuje się je najczęściej w rozwiązaniach przemysłowych, typu maszyny przemysłowe, elementy wykonawcze, itp.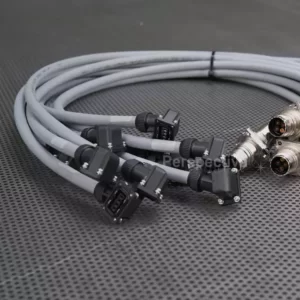
Wiązka elektryczna Junior Timer i Harting
Produkcja wiązek elektrycznych ze złączami Junior timer to standard, który pozwala uzyskać doskonałe parametry szczelności w zastosowaniach przemysłowych i motoryzacji. Harting zapewnia doskonałą trwałość.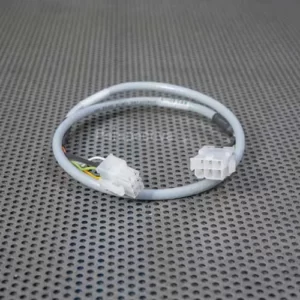
Wiązka elektryczna ze złączami M12 i Molex
Złącza M6, M8, M12 oraz rodzina złączy Molex to doskonale znane i rozpowszechnione standardy przemysłowe do zastosowań w transmisji sygnałów. Produkowane wiązki kablowe ze złączem M12 i Molex sprawdzają się m.in. w automatyce i robotyce.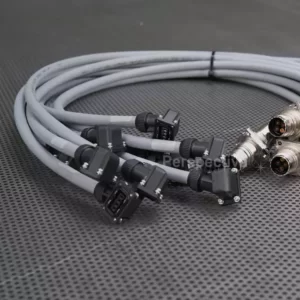
Wiązka elektryczna ze złączem M-23
Standard M23 pozwala na tworzenie trwałego i niezawodnego połączenia w przemyśle szeroko pojętej robotyki. Z drugiej strony często stosuje się złącza enkoderowe. Produkcja wiązek kablowych (hybrydowa) ze złączem M-23 realizowana jest według wymogów i specyfikacji klienta.Co to są wiązki elektryczne?
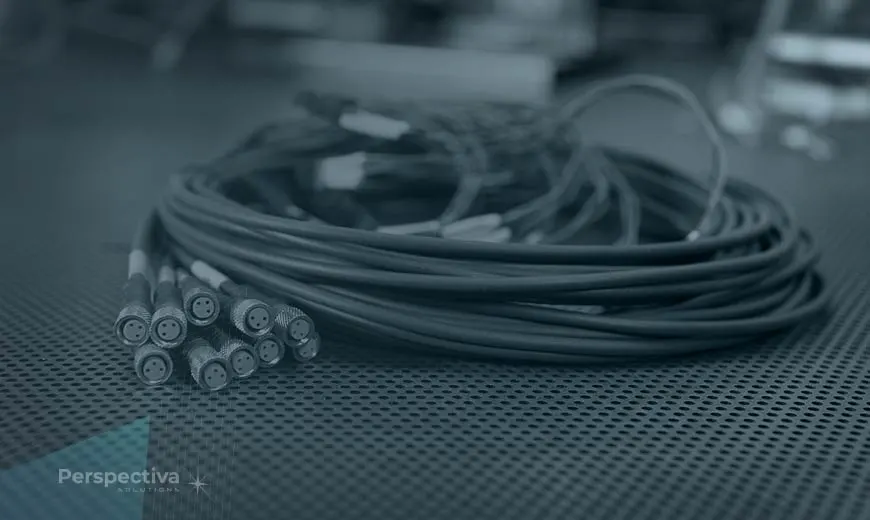
Wiązki elektryczne, nazywane również wiązkami kablowymi lub wiązkami przewodów, to system elektrycznych przewodów lub kabli, które zostały połączone i zgrupowane w celu przesyłania energii elektrycznej lub sygnałów elektrycznych i informacyjnych pomiędzy różnymi elementami systemu elektrycznego.
Wiązki elektryczne są starannie zaprojektowane i wykonane, aby zapewnić niezawodną i bezpieczną transmisję energii i sygnałów, minimalizując ryzyko zakłóceń i awarii. Ich odpowiednie zabezpieczenia i izolacje są kluczowe dla zapewnienia bezpiecznej pracy urządzeń elektrycznych i systemów.
Czym różni się wiązka elektryczna od wiązki kablowej?
Wiązka elektryczna to system skomplikowanych połączeń, zestaw przewodów, kabli, złączy, zacisków i innych elementów elektrycznych, pozwalających przesyłać prąd elektryczny lub sygnały informacyjne. Wszystkie te elementy zostają połączone razem już na etapie procesu projektowania wiązki elektrycznej, który uwzględnia warunki pracy i jej zastosowane.
Różnica między wiązką elektryczną a wiązką kablową leży w zakresie terminologicznym i konkretnych zastosowaniach. Oba terminy odnoszą się do zestawu przewodów lub kabli, które są złączone w celu przesyłania energii elektrycznej, sygnałów lub danych w określonych aplikacjach. Wiązki elektryczne i kablowe są kluczowymi elementami w instalacjach elektrycznych i elektronicznych, umożliwiając poprawne funkcjonowanie i niezawodność urządzeń. W praktyce bardzo często pojęcia te są używane zamiennie.
Zastosowanie wiązek elektrycznych w sektorach przemysłu
Wiązki elektryczne mogą być stosowane do zasilania maszyn, urządzeń, systemów itp., a także do przesyłania sygnałów sterujących i informacyjnych. Wiązki elektryczne są również ważnym elementem w automatyzacji procesów przemysłowych.
- Automatyka przemysłowa
- Samochody, motoryzacja
- Budownictwo – maszyny budowlane
- Rolnictwo – maszyny rolnicze
- Elektronika
- Przemysł elektryczny
- Przemysł lotniczy
- Przemysł kosmiczny
- Przemysł medyczny
- Przemysł komunikacyjny (kolejnictwo, komunikacja miejska)
- Przemysł zbrojeniowy
- Przemysł stoczniowy
Struktura wiązek elektrycznych
- Przewody kablowe – Elementy główne wiązki, które transmitują energię elektryczną lub sygnały. Mogą mieć różne przekroje i kolory, co ułatwia identyfikację funkcji poszczególnych przewodów.
- Izolacja przewodu – Warstwa ochronna wokół przewodów, zapewniająca izolację elektryczną oraz ochronę przed uszkodzeniami mechanicznymi lub środowiskowymi.
- Złącza – Punkty, w których przewody są łączone ze sobą lub do komponentów. Mogą to być wtyczki, gniazda, zaciski lub inne rodzaje złączy.
Dodatkowe komponenty
Wiązki elektryczne mogą zawierać różnorodne komponenty, które zwiększają ich funkcjonalność i wydajność. Niektóre z kluczowych komponentów to:
- Zabezpieczenia – Elementy, takie jak bezpieczniki i przerywacze, które chronią wiązkę i podłączone urządzenia przed przeciążeniami prądowymi lub zwarciami.
- Więzy, opaski, taśmy – Służą do utrzymania wiązki w porządku oraz zapewnienia stabilności mechanicznej. Mogą być elastyczne lub nieelastyczne, w zależności od potrzeb.
- Oznaczenia – Etykiety, znaczniki lub kolory służące do identyfikacji przewodów i funkcji w wiązce kablowej.
Projektowanie wiązek elektrycznych
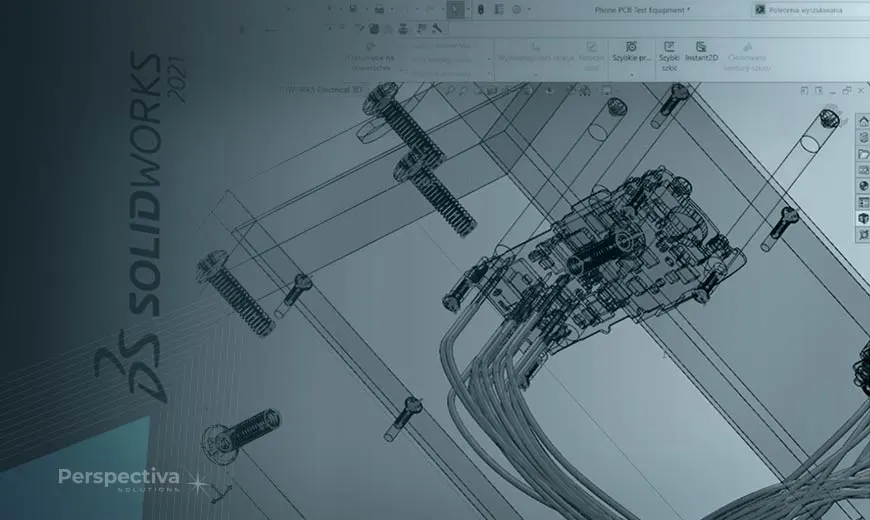
Niezawodne projektowanie wiązek elektrycznych odgrywa fundamentalną rolę we współczesnych systemach automatyki i maszyn. To istotny aspekt, który wpływa na sprawność i bezpieczeństwo urządzeń w wielu dziedzinach, takich jak motoryzacja, lotnictwo, przemysł elektroniczny oraz telekomunikacja. Wprowadzenie precyzyjnych i starannie przemyślanych rozwiązań w projektowaniu wiązek elektrycznych ma kluczowe znaczenie dla zapewnienia nieprzerwanego funkcjonowania systemów i minimalizowania ryzyka awarii. Niesprawne lub źle zaprojektowane wiązki kablowe mogą powodować awarie systemów, co w skrajnych przypadkach może skutkować poważnymi stratami finansowymi lub zagrożeniem dla życia ludzi.
Zobacz także: Niezawodność wiązki kablowej dla ładowarki do samochodów elektrycznych.
Dlaczego niezawodny projekt wiązki elektrycznej jest tak istotny? Ważne jest, aby zrozumieć, że nie tylko jakość poszczególnych komponentów wiązki elektrycznej ma znaczenie, ale także sposób ich projektowania i łączenia oraz stosowania zabezpieczeń. Projektowanie elektryczne obejmuje kompleksowy proces uwzględniający optymalne trasy przewodów, właściwe oznaczenia elektryczne oraz zastosowanie najnowszych norm i standardów. Zrozumienie zasad projektowania instalacji elektrycznych oraz skrupulatne wdrożenie tych zasad może znacząco wpłynąć na trwałość, wydajność i bezpieczeństwo całego systemu.
Projektowanie wiązek elektrycznych dla klienta
Projektowanie wiązek elektrycznych dla klienta to proces tworzenia indywidualnych rozwiązań dopasowanych do specyficznych potrzeb i wymagań klienta. Wiązki elektryczne zawsze wykonywane są ściśle według technicznych i jakościowych wytycznych dostarczonych przez klienta. W końcu to klient najlepiej wie, w jaki sposób działa dane urządzenie elektryczne, do którego chce zastosować wiązkę kablową. Zobacz jak prawidłowo dobrać wiązkę elektryczną.
Projektując wiązki przewodów elektrycznych, należy uwzględnić wiele czynników, takich jak rodzaj i wielkość przewodów, rodzaj złączy, sposób łączenia elementów, a także kryteria estetyczne i ergonomiczne.
Programy do projektowania systemu przewodów wiązek elektrycznych
Odpowiednie oznaczenia elektryczne w projekcie wiązki kablowej są kluczowe dla zminimalizowania ryzyka błędów podczas montażu i konserwacji. Poprawne identyfikowanie poszczególnych przewodów oraz ich przeznaczenia ułatwia diagnostykę i naprawy, co ma istotne znaczenie w przypadku ewentualnych problemów. Dlatego też, korzystanie z zaawansowanych narzędzi, takich jak dedykowany program do projektowania wiązek elektrycznych, może przyspieszyć i usprawnić proces tworzenia kompleksowych rozwiązań.
Jest to zaawansowany program do projektowania wiązek elektrycznych opracowany przez firmę Dassault Systèmes. To potężne oprogramowanie do projektowania 3D, oferujące moduł przeznaczony specjalnie do projektowania wiązek kablowych. Zapewnia zaawansowane narzędzia do tworzenia, zarządzania i analizy wiązek elektrycznych w różnych branżach, takich jak lotnictwo, automotive czy przemysł.
Jest to kompleksowe oprogramowanie do projektowania elektrycznych i elektronicznych systemów w tym także wiązek kablowych. Umożliwia integrację danych, optymalizację trasy wiązek kablowych oraz generowanie dokumentacji technicznej.
SolidWorks Electrical - program jest częścią rodziny SolidWorks i zapewnia funkcje do projektowania elektryki w tym projektowania wiązek elektrycznych wraz z utworzeniem BOM - listy materiałowej. Jest to narzędzie na którym nasza firma aktualnie pracuje i które możemy polecić.
Zobacz także: Zalety projektowania wiązek kablowych w SolidWorks.
to wyspecjalizowana wersja programu AutoCAD dostosowana do projektowania instalacji elektrycznych, w tym do projektowania wiązek przewodów i kabli. Jest to wersja programu AutoCAD dedykowana projektowaniu instalacji elektrycznych i wiązek elektrycznych. Umożliwia projektowanie 2D, zarządzanie bibliotekami symboli i generowanie raportów.
To oprogramowanie do projektowania elektryki w tym projektowania wiązek elektrycznych. Umożliwia tworzenie schematów i rysunków technicznych, zarządzanie danymi i generowanie dokumentacji.
Zastanawiasz się jaki program wybrać do projektowania wiązek elektrycznych?
Wszystkie wymienione programy są używane w różnych branżach i oferują zaawansowane funkcje. Wszystkie także pozwalają na efektywne projektowanie, zarządzanie i dokumentowanie wiązek elektrycznych w kompleksowych projektach. Wybór konkretnego programu może zależeć od potrzeb i preferencji użytkownika, a także od branży, w której zostanie wykorzystany w celu zaprojektowania systemu instalacji wiązek kablowych. Bazując na naszym wieloletnim doświadczeniu, proponujemy projektowanie wiązek elektrycznych oraz dedykowaną produkcję wiązek elektrycznych pod zamówienie, doradzając najlepsze, optymalne i najbardziej efektywne wiązki kablowe.
Tworzenie prototypu wiązki elektrycznej
Tworzenie prototypu wiązki elektrycznej to kluczowy krok w procesie rozwoju produktu elektrycznego. Pomaga on zminimalizować ryzyko błędów i zapewnia, że finalna wiązka będzie działać zgodnie z oczekiwaniami. Niezależnie od tego, czy planujesz stworzyć innowacyjne urządzenie, czy też doskonalić istniejący produkt, prototypowanie wiązki elektrycznej jest niezbędne, aby zapewnić niezawodność, efektywność i bezpieczeństwo działania elektrycznych systemów.
Po wykonaniu projektu, produkcja każdej wiązki rozpoczyna się od tworzenia prototypu wiązki kablowej. Inżynierowie przygotowują schemat montażowy oraz sprawdzają parametry połączeń elektrycznych tak, aby odpowiadały wymaganiom urządzenia, w którym wiązki kablowe zostaną zamontowane. Gdy mamy pewność, że prototyp spełnia wymogi jakości projektu wiązki elektrycznej do urządzenia, możemy rozpocząć produkcję seryjną okablowania.
Warto także wspomnieć o wymogu staranności i dokładności podczas tworzenia prototypu, ponieważ może to znacząco wpłynąć na jakość i niezawodność twego projektu.
Dlaczego warto tworzyć prototypy wiązki elektrycznej?
- Sprawdzanie funkcjonalności: Tworzenie prototypu wiązki elektrycznej pozwala na weryfikację działania systemu przed pełnym wdrożeniem. Możesz upewnić się, że wszystkie połączenia są poprawne i że urządzenie działa zgodnie z założeniami.
- Optymalizacja kosztów: Prototypy pozwalają na wykrycie ewentualnych problemów już na wczesnym etapie projektu, co minimalizuje koszty napraw i zmian w późniejszych fazach produkcji.
- Doskonalenie projektu: Dzięki prototypowi możesz dokładnie przeanalizować wygląd i układ wiązki elektrycznej. To daje możliwość wprowadzenia ulepszeń i doskonałego dopracowania projektu.
- Testowanie wytrzymałości i niezawodności: Prototyp pozwala na przeprowadzenie testów wytrzymałościowych i niezawodnościowych, co jest kluczowe, szczególnie w przypadku urządzeń używanych w trudnych warunkach.
Co to jest BOM materiałowy?
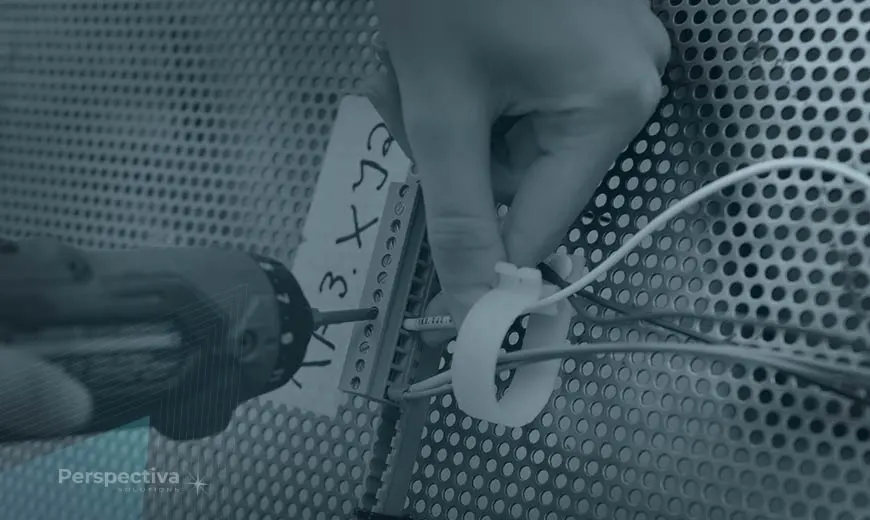
Bom definicja listy materiałowej
Lista materiałowa (BOM – ang. Bill of Materials) wiązki kablowej to dokument zawierający szczegółową listę wszystkich materiałów, komponentów i elementów elektrycznych wymaganych do produkcji lub montażu danej wiązki kablowej. BOM produkcyjny zawiera także kluczowe informacje o logistyce tj. informację o potrzebnych ilościach, dostawcy. Zawiera także referencje do rysunku technicznego wiązki kablowej wskazujące miejsce użycia danego komponentu. Różne narzędzia programowe, takie jak np. SolidWorks, udostępniają funkcje tworzenia zestawień materiałów z eksportem do pdf i zarządzania nimi. Dostępne są również szablony do wydajnego tworzenia zestawień materiałowych.
BOM jest niezbędny w procesie projektowania, wytwarzania i utrzymania wiązki kablowej, ponieważ pozwala na precyzyjne określenie ilości i typów potrzebnych elementów, a także kontrolę jakości i spójność produkcji. Jest także niezbędnym źródłem informacji dla działu zakupów.
Jakie informacje zawiera BOM materiałowy dla wiązki kablowej?
Chcesz wiedzieć co zawiera zestawienie materiałów? Poniżej przedstawiamy przykład listy materiałowej dla montażu wiązki elektrycznej. Dowiedz się, jakie informacje zawiera bom materiałowy:
- Przewody i kable – Zawiera informacje o typach kabli i przewodów, ich długościach, przekrojach i kolorach.
- Złącza i konektory – Określa rodzaj, typ, ilość i sposób połączenia złączy w wiązce kablowej.
- Terminale (tzw. piny lub styki) – Niektóre złącza i styki są dostarczane oddzielnie. Konieczne jest zatem wskazanie informacji identyfikujących komponent, dostawcę oraz faktycznie potrzebne ilości do wykonania kompletów przewodów wiązki elektrycznej.
- Izolacje i osłony – Informuje o materiałach izolacyjnych, osłonach i osłonach elektromagnetycznych, które zabezpieczają przewody wiązki elektrycznej.
- Elementy montażowe – Wskazuje na wszelkie elementy, które będą używane do montażu i mocowania wiązki kablowej, takie jak taśmy, opaski, zaciski itp.
- Etykiety i oznaczenia – Może zawierać informacje o etykietach i oznaczeniach, które mają być stosowane w celu identyfikacji poszczególnych przewodów lub złączy.
- Uszczelki i zaślepki – W celu zapewnienia hermetyczności wiązki kablowej, szczególnie w obszarze złączy stosuje się specjalne uszczelki na terminale. A jeśli w złączu zostaje puste pole bez terminala, bardzo często stosuje się dedykowane zaślepki.
- Elementy dodatkowe – W przypadku bardziej skomplikowanych wiązek kablowych, lista materiałowa może zawierać informacje o dodatkowych elementach, takich jak przełączniki, diody, bezpieczniki itp.
Jakie jest znaczenie zestawienia komponentów w kontekście procesów produkcyjnych i produkcji wiązek przewodów?
Lista materiałowa wiązki kablowej służy jako punkt odniesienia dla działów zakupów, produkcji i kontroli jakości, zapewniając spójność i precyzję podczas całego procesu wytwarzania lub montażu. BOM służy jako lista materiałowa ułatwiając również zarządzanie zapasami, prognozowanie kosztów i optymalizację projektu wiązki kablowej pod kątem wydajności, niezawodności i kosztów produkcji.
Podsumowując, zestawienie materiałowe jest niezbędnym dokumentem, który zapewnia płynne i dokładne procesy produkcyjne, efektywną komunikację i zoptymalizowany projekt produktu. Odgrywa fundamentalną rolę w różnych aspektach produkcji, od zaopatrzenia po kontrolę jakości.
Cięcie i odizolowywanie przewodów wiązek kablowych
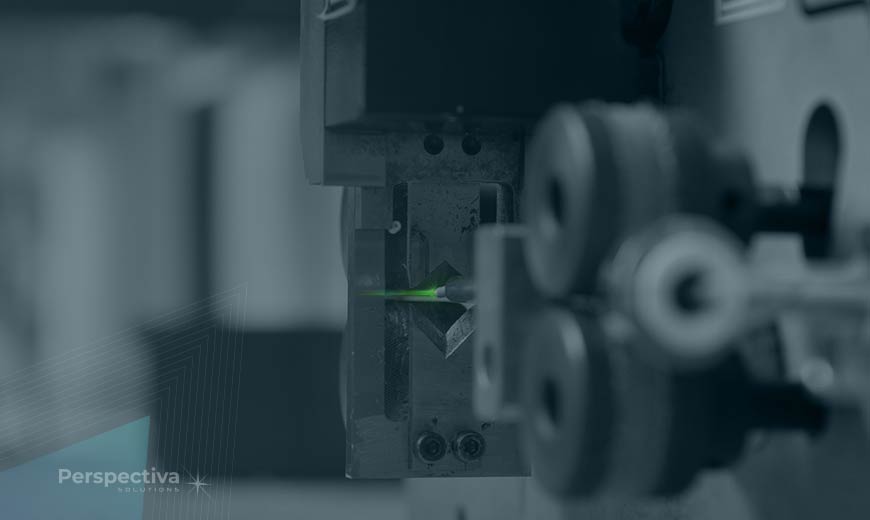
W przypadku przewodów o większej ilości żył lub kiedy są wykonane z materiałów trudno obrabialnych, cięcie wiązki kablowej dzieli się na dwa etapy.
- Pierwszy z nich to automatyczne zdjęcie izolacji zewnętrznej podczas cięcia.
- Drugi etap to ręczne odizolowanie żył wewnętrznych, które pozwala także na skręcenie żył przewodu, aby móc uzyskać nie postrzępiony, jednolity koniec wiązki elektrycznej.
Automatyczne maszyny do cięcia kabli i odizolowania przewodów jednożyłowych
Automatyczna maszyna do cięcia kabli i odizolowania przewodów jednożyłowych to zaawansowane urządzenie, które znacznie ułatwia i usprawnia proces powstawania wiązki elektrycznej. Dzięki swojej automatycznej funkcjonalności zapewnia dokładne cięcie i odizolowanie w szybkim tempie, minimalizując czas i wysiłek potrzebny do wykonania wiązki kablowej.
Obsługa tej maszyny jest łatwa i intuicyjna. Pracownik musi jedynie podłączyć urządzenie, umieścić przewód wiązki kablowej w odpowiednim miejscu na maszynie, ustawić odpowiednie parametry cięcia i odizolowania, a następnie uruchomić proces. Automatyczna maszyna przeprowadzi resztę pracy, dokładnie tnie kabel na żądaną długość i precyzyjnie odizolowuje koniec przewodu.
Kluczowe zalety korzystania z automatycznej maszyny do cięcia kabli i odizolowania przewodów jednożyłowych to:
- Wydajność: Dzięki swoim automatycznym funkcjom, maszyna może obsłużyć duże ilości wiązek kablowych w krótkim czasie, co znacznie zwiększa wydajność produkcji.
- Precyzja i powtarzalność: Automatyczne maszyny są znane z precyzyjnego cięcia i odizolowania wiązek kablowych, co pozwala na uzyskanie doskonałej jakości montażu. Ponadto, automatyczny charakter maszyny gwarantuje powtarzalność procesu, eliminując ryzyko błędów ludzkich.
- Bezpieczeństwo: Operator jest chroniony przed ryzykiem skaleczenia, które może wystąpić podczas ręcznego cięcia i odizolowania okablowania.
- Minimalne straty materiałowe: Dzięki precyzyjnemu cięciu minimalizuje się straty materiału, co przekłada się na oszczędności w produkcji wiązek elektrycznych.
Dla zachowania bezpieczeństwa i efektywności użytkowania, ważne jest, aby operatorzy byli odpowiednio przeszkoleni w obsłudze maszyny, przestrzegali zasad bezpieczeństwa oraz regularnie przeprowadzali konserwację i serwisowanie urządzenia.
Automatyczne maszyny do cięcia kabli i odizolowania przewodów jednożyłowych są dostępne w różnych typach i wariantach, zależnie od potrzeb i zastosowań wiązek kablowych.
Oto kilka typów oraz wybrane, najczęściej spotykane rodzaje tych maszyn:
- Automatyczne maszyny do cięcia kabli i odizolowania jednożyłowych.
- Komputerowo sterowane maszyny do cięcia i odizolowania, które pozwalają na programowanie wielu różnych długości i rozmiarów kabli oraz rodzajów izolacji.
- Maszyny z funkcją rozpoznawania i przycinania, które wykorzystują zaawansowane sensory do automatycznego rozpoznawania długości i wymiarów wiązki kablowej przed odizolowaniem.
- Maszyny wielofunkcyjne, które łączą w sobie różne narzędzia, umożliwiające cięcie, odizolowanie i podział wiązki kablowej w jednym urządzeniu.
Automatyczna maszyna do cięcia kabli i odizolowania przewodów jednożyłowych jest niezastąpionym narzędziem w przemyśle elektrycznym i elektromechanicznym, przyczyniając się do poprawy jakości pracy, oszczędności czasu i materiałów przy produkcji wiązek elektrycznych.
Etykietowanie i znakowanie wiązki elektrycznej
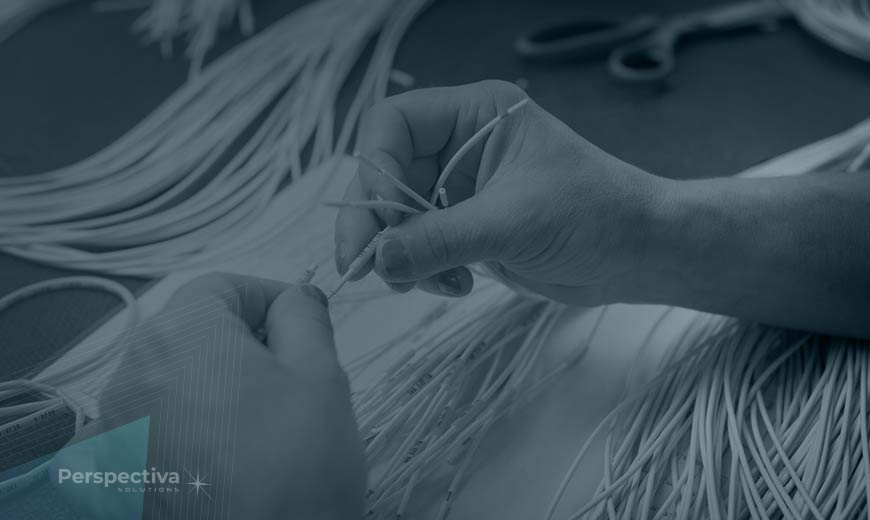
Działanie etykietowania i znakowania wiązki elektrycznej ma na celu przyspieszenie procesu identyfikacji typu danego kabla. Ułatwia to także późniejszy proces montażu u klienta oraz serwisowanie i znalezienie przyczyny ewentualnej awarii wiązki kablowej.
- brązowy lub czarny – przewód fazowy,
- niebieski – przewód neutralny,
- żółto–zielony – przewód ochronny PE,
- czerwony – przewód prądu stałego plus,
- czarny lub niebieski – przewód prądu stałego minus.
Zdarza się jednak, że kodowanie kolorami wiązki kablowej jest niewystarczające, aby można było je uznać za odpowiednią, jednoznaczną informację. Stosuje się wówczas oznaczniki drukowane, najczęściej wykonane na samoprzylepnej taśmie, rurce termokurczliwej, tzw. etykiecie samolaminującej lub gładkiej rurce osłonowej. Taki sposób pozwala na wykorzystanie kilku kolorów oznaczników wiązki elektrycznej, jak i wykonanego na nich nadruku, a przede wszystkim umożliwia umieszczenie dowolnej, pożądanej przez klienta treści tekstowej.
Jak przebiega proces znakowania przewodów elektrycznych?
Najpopularniejszym i najprostszym sposobem na oznaczanie poszczególnych przewodów w wiązce elektrycznej jest użycie różnych kolorów izolacji omówionych powyżej. Można jednak, zastosować do tego oznaczniki wykonane z rurek termokurczliwych, które pełnią funkcję izolacji. Nasza firma posiada dedykowane drukarki do etykiet oraz znakowarkę laserową, które świetnie sprawdzają się w prawidłowym oznaczeniu przewodów wiązek kablowych.
Drukarki etykiet stosowane do drukowania oznaczeń na rurkach PVC używanych do identyfikacji i oznaczania wiązek kablowych różnią się w zależności od potrzeb i preferencji użytkownika.
Rodzaje drukarek używane w procesie znakowania przewodów kablowych:
- Drukarki termotransferowe – są jednymi z najczęściej używanych urządzeń do drukowania etykiet na rurkach PVC, tasiemkach oraz rurkach termokurczliwych do oznaczania wiązek kablowych. Wykorzystują one technologię termotransferową, która gwarantuje trwałe, odporne na ścieranie i wysokiej jakości oznaczenia, kluczowe przy identyfikacji wiązek kablowych. Materiały termotransferowe są dostępne w różnych kolorach, co umożliwia tworzenie kolorowych etykiet z różnymi informacjami.
- Drukarki termiczne – są prostsze w obsłudze niż drukarki termotransferowe, ponieważ nie wymagają używania taśm, a obraz jest bezpośrednio wydrukowany na etykiecie przy użyciu ciepła. Są one również wygodne do drukowania na niewielkich ilościach etykiet.
- Drukarki do transferu termicznego – te drukarki łączą w sobie cechy drukarek termicznych i termotransferowych, wykorzystując technologię transferu termicznego do drukowania na różnych materiałach, w tym na rurkach PVC wykorzystywanych w instalacjach przewodów elektrycznych.
- Drukarki atramentowe (inkjet) – chociaż mniej popularne, mogą być używane w niektórych przypadkach. Wykorzystują one technologię atramentową do nanoszenia obrazu na powierzchnię etykiety.
- Drukarki laserowe – stosowane są raczej do drukowania etykiet na rurkach PVC, ale w niektórych przypadkach mogą być używane do precyzyjnego i trwałego oznaczania bezpośrednio na przewodzie wiązki kablowej.
Wiązki kablowe przewodów elektrycznych oznacza się także za pomocą liter i cyfr. Znakowanie takie informuje o budowie przewodu i zwykle składa się z trzech części:
- Literowa – informuje o konstrukcji i materiale żyły przewodzącej, materiale wykorzystanym do stworzenia izolacji i powłoki, a także inne informacje uzupełniające,
- Cyfrowa – informuje o napięciu znamionowym izolacji wiązki kablowej,
- Cyfrowa – informuje o liczbie i przekroju żył przewodzących wiązki elektrycznej.
Zaciskanie lub lutowanie terminali wiązek kablowych
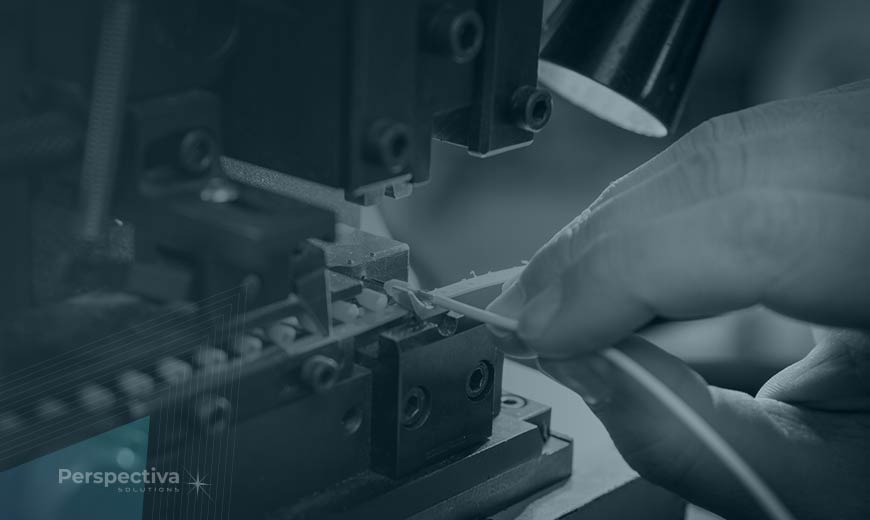
Prawie w każdej wiązce elektrycznej znajdują się terminale, czyli różnego rodzaju styki. Czasem zwane także pinami.
Wyróżniamy dwa podstawowe rodzaje styków – otwarte (ang. open barrel) i zamknięte (ang. closed barrel).
Czynność zaciskania można wykonywać przy pomocy narzędzi ręcznych, ale najlepszą opcją jest zastosowanie prasy wraz z aplikatorami do konektorów. Tradycyjne, ręczne metody zaciskania konektorów, stają się coraz bardziej niepraktyczne i czasochłonne w obliczu rosnącej złożoności systemów elektrycznych. Prasa elektryczna, pneumatyczna lub pół pneumatyczna w sposób w pełni zautomatyzowany pozwala na łączenie przewodów elektrycznych oraz wiązek kablowych z komponentami elektronicznymi. Automatyczne maszyny reprezentują natomiast nowoczesne podejście, które wykorzystuje technologiczne rozwiązania, aby spełnić wysokie wymagania produkcji i montażu wiązek elektrycznych.
Maszyny do zaciskania terminali/konektorów
Wraz z rosnącym zapotrzebowaniem na zaawansowane i złożone systemy elektryczne, automatyczne maszyny do zaciskania końcówek wiązek kablowych tj. konektorów stały się niezwykle ważnymi narzędziami w przemyśle elektrycznym i elektronicznym. Te innowacyjne urządzenia zapewniają efektywne i precyzyjne zaciskanie konektorów na przewodach w wiązce elektrycznej, co jest kluczowe dla zapewnienia niezawodnej i bezpiecznej pracy różnego rodzaju urządzeń, pojazdów, samochodów, maszyn oraz systemów.
Dzięki wyposażeniu w zaawansowane systemy kontroli, czujniki oraz programowalne układy, maszyny te pozwalają na indywidualne dostosowanie parametrów zaciskania dla różnych typów terminali, konektorów i przewodów. Tym samym umożliwiają produkcję wiązek elektrycznych o jednolitej i niezawodnej jakości, co jest kluczowe dla branż, gdzie bezpieczeństwo i precyzja działania mają najwyższy priorytet.
Automatyczne maszyny do zaciskania konektorów mają pozytywny wpływ na wydajność procesów produkcyjnych, umożliwiając szybkie i skuteczne zaciskanie konektorów w dużej ilości wiązek elektrycznych w krótkim czasie. To z kolei przekłada się na obniżenie kosztów produkcji oraz skrócenie czasu wprowadzenia produktu na rynek.
Typy automatycznych maszyn do zaciskania terminali/konektorów
Automatyczne maszyny do zaciskania terminali/konektorów w wiązkach elektrycznych są dostępne w różnych typach, zależnie od potrzeb i specyfikacji produkcji wiązek kablowych. Oto kilka popularnych typów automatycznych maszyn do zaciskania konektorów:
- Zaciskanie konektorów wierzchołkowych
Te maszyny są przeznaczone do zaciskania konektorów wierzchołkowych, czyli takich, które mają zakończenie w formie wierzchołka lub końcówki do zaciskania. Wykorzystują różne mechanizmy do precyzyjnego i mocnego zaciskania konektorów na przewodach wiązek kablowych. - Zaciskanie konektorów skręcanych
Te maszyny są dedykowane do zaciskania konektorów skręcanych, które wymagają odpowiedniego skręcenia przewodów wiązki kablowej wewnątrz terminala/konektora, aby osiągnąć trwałe połączenie. - Zaciskanie konektorów izolowanych
Te maszyny są wyposażone w dodatkowe narzędzia, które umożliwiają nie tylko zaciskanie konektorów z dodatkowymi elementami izolującymi, ale również odcięcie ich od szyny nośnej, co pozwala na oszczędność czasu i zapewnia estetyczny wygląd wiązki elektrycznej. - Zaciskanie konektorów IDC (Insulation Displacement Connectors)
Te maszyny są specjalnie zaprojektowane do zaciskania konektorów IDC, które wykorzystują technologię przenikania izolacji przewodu, aby utworzyć połączenie elektryczne. Zastosowanie takich złączy powoduje, że zostaje dokonana perforacja izolacji podczas czynności zaciskania, jest to tzw. IDC (ang. insulation displacement connection). Najczęściej stosuje się je przy przewodach wstążkowych wiązek kablowych. Jest to odmienne rozwiązanie, którym są złącza niewymagające odizolowywania. Pozwalają one na proste uzyskanie wielożyłowego połączenia, głównie do kabli, które nie potrzebują dużych przekrojów przewodów. - Zaciskanie konektorów na listwie zaciskowej
Te maszyny są przeznaczone do zaciskania konektorów na listwach zaciskowych, które są często stosowane w panelach sterujących i innych urządzeniach elektrycznych. - Zaciskanie konektorów na przewodach płaskich
Te maszyny są dedykowane do zaciskania konektorów na płaskich przewodach, które wymagają specjalnych mechanizmów do precyzyjnego i równomiernego zaciskania. - Zaciskanie konektorów specjalistycznych
Niektóre maszyny są dostosowane do zaciskania konektorów o specjalistycznych kształtach lub do zastosowań w określonych branżach.
Wybór odpowiedniego typu maszyny do zaciskania konektorów zależy od konkretnych wymagań produkcji i rodzaju konektorów używanych w wiązkach elektrycznych. Warto inwestować w zaawansowane i wysokiej jakości maszyny, które zapewnią precyzyjne zaciskanie końcówek terminali/konektorów, co przekłada się na trwałe i niezawodne połączenia w wiązkach elektrycznych.
Funkcje automatycznych maszyn do zaciskania terminali/konektorów
Automatyczne maszyny do zaciskania konektorów w wiązkach elektrycznych oferują wiele zaawansowanych funkcji, które mają na celu zapewnienie precyzyjnego, niezawodnego i efektywnego zaciskania konektorów. Poniżej przedstawiono kilka kluczowych funkcji, które można znaleźć w tych maszynach:
- Programowalne ustawienia: Automatyczne maszyny do zaciskania konektorów posiadają programowalne ustawienia, które umożliwiają dostosowanie procesu zaciskania do różnych typów terminali/konektorów i przewodów kablowych. Operator może łatwo zmieniać parametry zaciskania, takie jak siła nacisku, czas trwania zaciskania i wielkość zacisku, co umożliwia elastyczność w produkcji a przede wszystkim umożliwia skrócenie czasów przestoju maszyn z powodu ich przezbrojeń.
- Kontrola nacisku:
Zaawansowane maszyny są wyposażone w systemy kontroli nacisku, które monitorują siłę nacisku podczas zaciskania. Dzięki temu możliwe jest precyzyjne i równomierne zaciskanie konektorów na przewodach wiązek elektrycznych, co minimalizuje ryzyko niewłaściwego połączenia. - Czujniki i systemy wizyjne:
W niektórych maszynach stosuje się czujniki i systemy wizyjne, które pomagają w identyfikacji i lokalizacji przewodów oraz konektorów. To umożliwia automatyczne dostosowanie maszyny do różnych rozmiarów i typów terminali/konektorów. - Detekcja błędów:
Automatyczne maszyny do zaciskania konektorów są wyposażone w funkcje detekcji błędów, które pozwalają na identyfikację i reagowanie na ewentualne problemy podczas zaciskania wiązek kablowych, na przykład przerywanie procesu w przypadku braku poprawnego zaciskania. - Systemy zabezpieczeń:
W celu zapewnienia bezpiecznej pracy maszyny, wiele modeli posiada systemy zabezpieczeń, takie jak osłony ABS, czujniki bezpieczeństwa i awaryjne wyłączniki, które chronią operatorów przed ryzykiem uszkodzeń. - Szybka zmiana narzędzi:
Niektóre maszyny są wyposażone w systemy szybkiej zmiany narzędzi, co pozwala na łatwe dostosowanie maszyny do różnych typów konektorów bez konieczności długiego czasu przestawiania. - Integracja z systemami automatycznymi:
Zaawansowane maszyny mogą być zintegrowane z systemami automatycznymi, takimi jak linie produkcyjne czy roboty, co umożliwia bezproblemowy przepływ pracy i zwiększenie wydajności produkcji.
Wszystkie te funkcje mają na celu zapewnienie wysokiej jakości i niezawodności zaciskania konektorów na wiązce elektrycznej, co jest kluczowe dla zapewnienia trwałych i bezpiecznych połączeń elektrycznych w różnych aplikacjach przemysłowych, motoryzacyjnych, elektronicznych i innych. Automatyczne maszyny do zaciskania konektorów są nie tylko bardziej efektywne, ale także pozwalają uniknąć błędów ludzkich i oszczędzić czas oraz koszty w procesie produkcji wiązek elektrycznych.
Przekrój metalograficzny zaciśniętego konektora
Przekrój metalograficzny to rodzaj przekroju konektora, który pozwala na ocenę geometrii zaciśniętego terminala, a tym samym, pośrednio, umożliwia ocenę poprawności procesu zagniatania wiązki kablowej.
W przypadku wiązek elektrycznych, wykonanie przekroju metalograficznego może dodatkowo pomóc w zrozumieniu struktury materiału, z którego wykonana jest wiązka elektryczna, oraz identyfikacji potencjalnych problemów związanymi z jakością materiału, takich jak niejednorodności, inkluzje, pory, mikropęknięcia, degradacja struktury itp. Pozwala to na ocenę, czy materiał jest odpowiednio przystosowany do zastosowania w danej aplikacji elektrycznej. Przekrój metalograficzny zaciśniętego konektora jest wykonywany w celu weryfikacji procesu zakuwania. Np.: jeżeli konektory przeznaczone są do wiązek elektrycznych używanych w branży motoryzacyjnej, gdzie w przypaku samochodów występują wymagania związane z trwałością i gazoszczelnością takiego zakucia.
Proces wykonania przekroju metalograficznego obejmuje kilka kroków, takich jak przygotowanie próbki wiązki kablowej(wycięcie, osadzenie w żywicy), szlifowanie, polerowanie, a następnie etap mikroskopowej analizy, często przy użyciu mikroskopu optycznego lub mikroskopu elektronowego. Badanie wykonywane jest w laboratorium,. Najpierw szlifowana jest powierzchnia przekroju, która po wytrawieniu kwasem, sprawdzana jest pod mikroskopem. Jeżeli zakuwanie przebiegło prawidłowo, na zewnątrz nie wydostają się żyły wiązki elektrycznej, a do środka nie wnika powietrze, to produkcja może być kontynuowana.
Dzięki badaniu przekroju metalograficznego można więc uzyskać cenne informacje na temat jakości i struktury mikroskopowej materiału, co jest kluczowe dla wielu dziedzin, w tym także dla analizy wiązek elektrycznych.
Taśmowanie lub wiązanie opaskami wiązki elektryczej
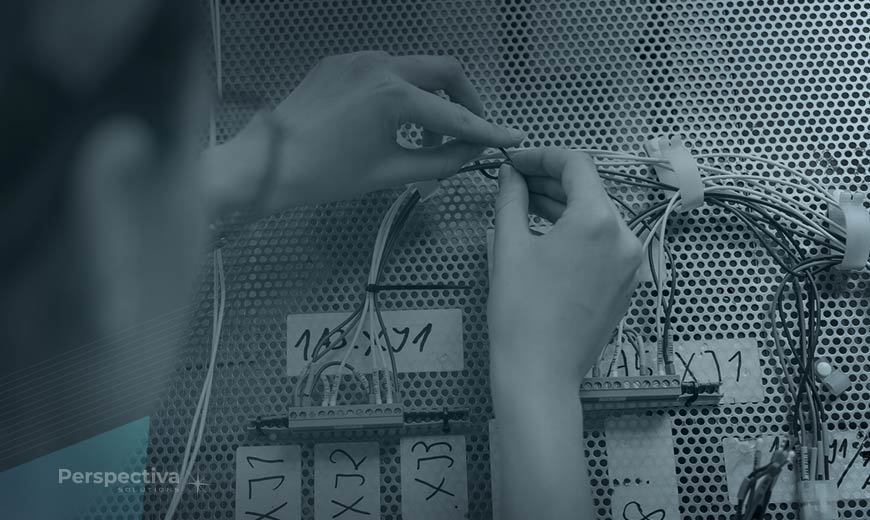
Głównym celem taśmowania i wiązania opaskami jest utrzymanie porządku pośród różnego rodzaju przewodów wchodzących w skład wiązki kablowej oraz zabezpieczenie ich przed ewentualnymi uszkodzeniami. Dodatkowo, proces ten umożliwia formowanie wiązki kablowej i utrzymanie jej w pożądanym kształcie. Dzięki takiemu działaniu można odpowiednio umocować, pogrupować i posegregować wiązki kablowe. Ułatwia to montaż i niweluje plątanie się kabli, co wpływa na bezpieczniejsze funkcjonowanie. Pozwala także zachować przejrzystość w razie późniejszej naprawy, czy serwisowania.
Do budowy wiązki kablowej stosuje się różnego rodzaju opaski, nierzadko o dedykowanym zastosowaniu, w zależności od warunków, w których będzie znajdować się przewód.
Istnieją trzy główne rodzaje opasek wiązek kablowych:
- ząbkowane wewnętrzne,
- ząbkowane zewnętrzne,
- całkowicie pozbawione ząbkowania.
Opaski ząbkowane wewnętrzne przeznaczone są do wiązania standardowych wiązek kablowych i przewodów, opaski ząbkowane zewnętrzne przeznaczone są dla kabli o delikatnej izolacji, ostatnie natomiast stosowane są do uporządkowania przewodów o dużych średnicach.
Ponadto, można wyróżnić także:
- opaski rozpinane (tymczasowe, wielokrotnego użytku),
- nierozpinane(stałe).
Podczas tego procesu wykonuje się również montaż osłon (np. rurek karbowanych, rurek gładkich, oplotów) oraz przy procesie taśmowania – peszli, oplotów naciąganych, sztucznych, metalowych.
Fixtury używane do produkcji i montażu wiązek kablowych
Fixtury w montażu gotowych wiązek kablowych odnoszą się do urządzeń lub narzędzi, które są używane do ułatwienia i usprawnienia procesu montażu wiązek elektrycznych. Te fixtury, zwane również jigami lub przyrządami montażowymi, mają na celu zapewnienie precyzyjnego i powtarzalnego położenia elementów wiązek elektrycznych, aby upewnić się, że montaż odbywa się zgodnie z wymaganiami technicznymi zawartymi w projekcie.
W praktyce fixtury mogą przybierać różne formy, od prostych i ręcznie wykonanych przyrządów po bardziej zaawansowane, zautomatyzowane systemy montażowe. Projektując fixtury, należy wziąć pod uwagę specyfikę wiązek elektrycznych, z którymi mają być używane, oraz procesu montażu.
Korzyści wynikające z użycia fixtur w montażu gotowych wiązek elektrycznych to m.in.:
- Precyzja: Fixtury pozwalają na dokładne umiejscowienie i połączenie przewodów, kabli, złączy i innych elementów, co minimalizuje ryzyko błędów i zapewnia wysoką jakość montażu wiązki elektrycznej.
- Powtarzalność: Dzięki fixturom proces montażu można łatwo powtarzać wielokrotnie, co jest kluczowe w produkcji seryjnej wiązek elektrycznych.
- Optymalizacja czasu: Fixtury pozwalają na efektywniejsze i szybsze wykonywanie montażu, co przekłada się na oszczędność czasu i kosztów pracy.
- Bezpieczeństwo: Poprawnie zaprojektowane fixtury mogą zabezpieczyć wiązki kablowe przed przypadkowymi uszkodzeniami, a także zapewnić ochronę przed porażeniem prądem.
- Ułatwienie testowania: Fixtury mogą ułatwić wykonywanie testów jakościowych wiązek elektrycznych po etapie montażu.
Ważne jest, aby osoby odpowiedzialne za montaż wiązek elektrycznych były odpowiednio przeszkolone w obsłudze i użyciu fixtur, aby móc w pełni wykorzystać ich potencjał i zapewnić najwyższą jakość i efektywność procesu montażu.
Międzyoperacyjna kontrola jakości produkcji
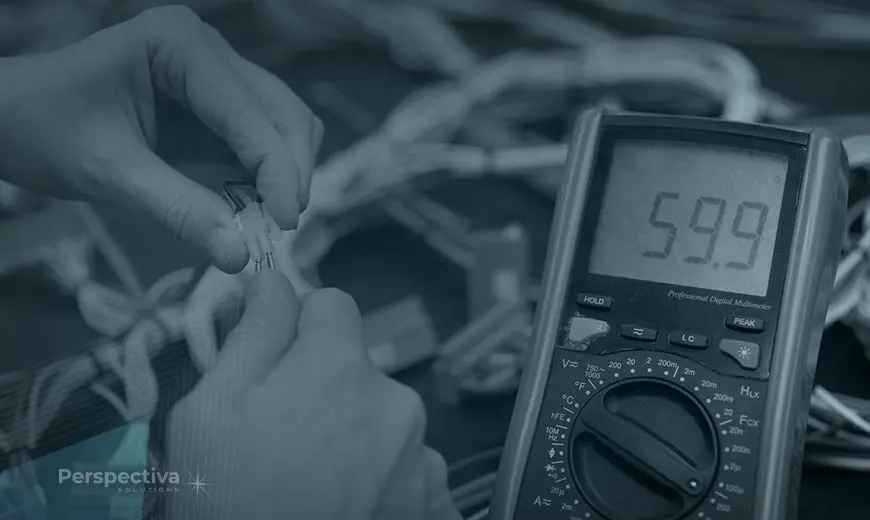
Narzędzia kontroli jakości w procesie budowy wiązki kablowej
Wdrożenie zaawansowanych narzędzi i metod kontroli jakości w międzyprocesowej kontroli jakości w produkcji wiązek elektrycznych przynosi wiele korzyści zarówno producentom, jak i odbiorcom produktów. Oto niektóre z kluczowych narzędzi i korzyści wynikających z wdrożenia zaawansowanych metod kontroli jakości wiązek kablowych:
- Systemy wizyjne: Wykorzystanie zaawansowanych systemów wizyjnych pozwala na automatyczne monitorowanie jakości połączeń, wykrywanie defektów oraz identyfikację nieprawidłowości wiązki kablowej w czasie rzeczywistym.
- Testery wytrzymałościowe: pozwalają na przeprowadzenie testów obciążeniowych, które sprawdzają wytrzymałość i niezawodność przewodów i konektorów podczas normalnego użytkowania wiązki elektrycznej.
- Systemy identyfikacji i etykietowania: Wdrożenie zaawansowanych systemów identyfikacji i etykietowania umożliwia precyzyjne oznaczanie i identyfikację wiązek elektrycznych, co ułatwia ich instalację i obsługę.
- Automatyczne maszyny do zaciskania konektorów: Zaawansowane maszyny do zaciskania konektorów pozwalają na precyzyjne i powtarzalne zaciskanie konektorów na przewodach wiązek elektrycznych. Dzięki temu eliminowane są błędy ludzkie i zapewniona jest jednolita jakość połączeń.
Montaż wiązek elektrycznych
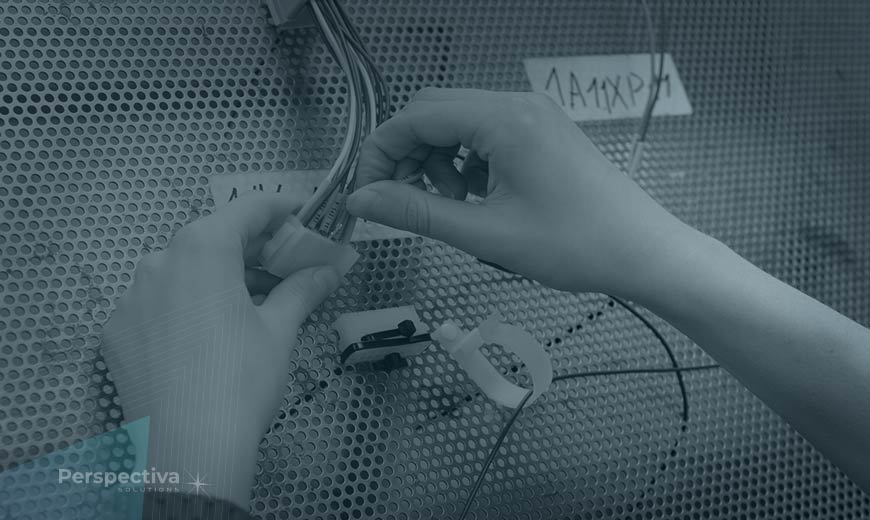
Jednym z ostatnich etapów produkcji wiązek elektrycznych jest ich montaż na dedykowanym stanowisku. Fikstury używane do montażu okablowania zależą od specyfiki projektu wiązki elektrycznej. Sam montaż złączy elektrycznych obejmuje zatrzaskiwanie styków w obudowach i konektorowanie, czyli osadzenie styku w złączu. Podczas tego procesu, sprawdzone zostaje dokładne umocowanie styku i odpowiednie usadzenie w złączu. Język i zapadka muszą zostać włożone do złącza w taki sposób, aby nie było luzu. Język i zapadka muszą zostać włożone do złącza w taki sposób zapewniający pozycjonowanie, które nie ulegnie samoistnemu demontażowi.
Warto dodać, że gdy zgodnie z zamówieniem klienta, produkcja wiązek elektrycznych oraz ich końcowy montaż może być przeprowadzany na maszynie/urządzeniu klienta. Różni się on stopniem skomplikowania w zależności od rodzaju maszyny, do której mocowana jest dana wiązka kablowa.
Co robi monter wiązek elektrycznych?
Chcesz wiedzieć na czym polega praca montera wiązek elektrycznych? Produkcja specjalistycznego okablowania to praca wymagająca znajomości zagadnień budowy wiązki kablowej, która wymaga szczególnego skupienia i precyzji. Monter wiązek elektrycznych to specjalista zajmujący się instalacją i montażem różnego rodzaju wiązek elektrycznych. Posługuje się schematem i na jego stanowisku odbywa się składanie wiązek kablowych zgodnie z zakładanymi planami technicznymi.
Jakie zadania wykonuje monter wiązek elektrycznych?
- Czytanie i interpretację schematów i planów technicznych
Monter wiązek elektrycznych musi umieć zrozumieć i odczytać złożone schematy elektryczne, które wskazują, jak połączyć różne elementy wiązki elektrycznej. - Przygotowanie okablowania i montaż wiązek elektrycznych
Monter musi przygotować odpowiednie długości kabli, przewodów, złączy(np. złączka kablowa zaciskowa) i osłon, a następnie skonstruować wiązkę zgodnie z wymaganiami technicznymi. - Podłączanie wiązek elektrycznych do urządzeń lub instalacji
Po wykonaniu wiązki kablowej, monter musi prawidłowo podłączyć ją do odpowiednich elementów, np. do silników, czujników, lamp, czy innych urządzeń elektrycznych. - Testowanie i diagnostyka
Po zakończeniu montażu wiązki kablowej, monter wykonuje testy, aby sprawdzić, czy wiązka elektryczna działa poprawnie i nie uległa awarii. W razie potrzeby, może także diagnozować i naprawiać ewentualne problemy. - Dbanie o bezpieczeństwo
Wszystkie połączenia wiązki elektrycznej muszą być wykonane zgodnie z odpowiednimi standardami i przepisami bezpieczeństwa, aby uniknąć ryzyka awarii lub zagrożenia pożarem czy porażeniem prądem. - Montaż osłon i zabezpieczeń
Monter wiązek kablowych musi także zadbać o właściwe zabezpieczenie wiązek elektrycznych przed uszkodzeniami mechanicznymi, wilgocią, czy innymi czynnikami zewnętrznymi.
Praca montera wiązek elektrycznych wymaga precyzji, dokładności i wiedzy z zakresu elektryki oraz technik montażu. Ten zawód jest szczególnie ważny w branżach takich jak motoryzacja, przemysł elektroniczny, przemysł lotniczy, a także w budownictwie i instalacjach elektrycznych gdzie późniejsza naprawa wiązki elektrycznej, która okaże się wadliwa, może być nie lada wyzwaniem.
Ile zarobi w Polsce monter wiązek elektrycznych?
Przeciętne zarobki montera wiązek elektrycznych w Polsce w ostatnich latach wynosiły od około 2500 do 4000 złotych brutto na miesiąc dla początkujących pracowników. Doświadczeni monterzy wiązek kablowych z dłuższym stażem oraz ci pracujący w bardziej wymagających branżach lub na stanowiskach z większą odpowiedzialnością mogą zarabiać nawet więcej, przekraczając 5000 złotych brutto na miesiąc.
Zobacz nasze ogłoszenia o pracę! Być może w tym momencie mamy etat dla montera wiązek elektrycznych i potrzebujemy właśnie Ciebie!
Końcowa kontrola jakości gotowej wiązki elektrycznej
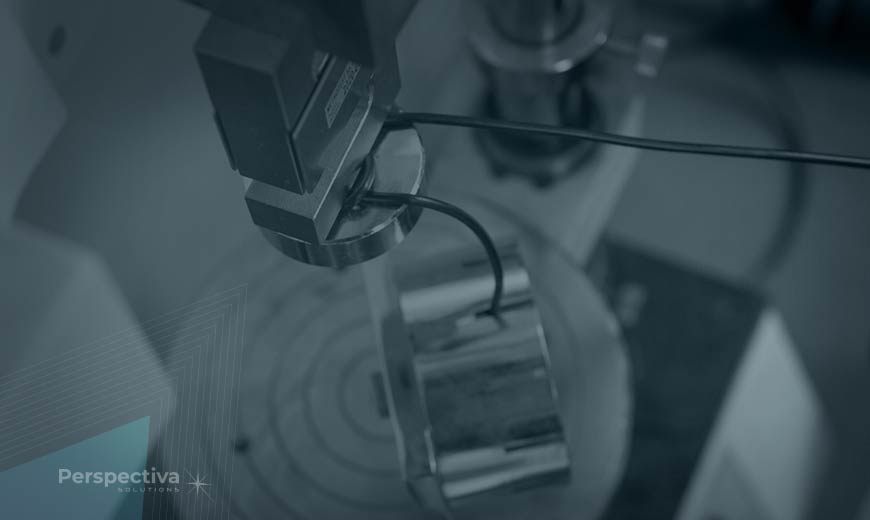
Końcowa kontrola jakości gotowej wiązki elektrycznej jest kluczowym etapem w procesie produkcji, który ma na celu zapewnienie doskonałej jakości i niezawodności finalnego produktu. Cały proces kontroli jakości wiązek kablowych jest skrupulatnie realizowany na każdym etapie produkcji okablowania. Weryfikowane są kluczowe aspekty, takie jak precyzyjność wymiarów cięcia, prawidłowe odizolowanie, geometryczne właściwości zaciśnięcia styku, a także pomiar siły zrywu przy wykorzystaniu specjalistycznego testera przewodów elektrycznych, oraz inne.
Decydującym elementem jest także ostateczna weryfikacja poprawności funkcjonowania i wykonania gotowych wiązek elektrycznych. Przed wysłaniem ich do klienta, przeprowadza się starannie przemyślaną, szczegółową kontrolę, w trakcie której dokładnie analizuje się wszelkie komponenty, połączenia, izolacje oraz identyfikatory. Końcowe testy obejmują ocenę prawidłowości połączeń elektrycznych, eliminację ewentualnych zwarć oraz zapewnienie ciągłości izolacji. Proces sprawdzania dotyczy nie tylko właściwości działania wiązek elektrycznych, lecz także ich dopasowania do urządzeń(kompatybilność z urządzeniem), do których zostaną podłączone.
Celem końcowej kontroli jakości jest upewnienie się, że każda wiązka elektryczna spełnia najwyższe standardy jakości oraz zgodna jest z wymaganiami specyfikacji technicznych. Skrupulatna analiza każdego detalu stanowi kluczowy punkt, biorąc pod uwagę zastosowanie wiązek elektrycznych w różnych dziedzinach, w tym w przemyśle motoryzacyjnym, elektronicznym, telekomunikacyjnym i innych, gdzie nawet drobne błędy mogą przynieść poważne skutki. Dlatego kluczowe testy, takie jak np. tester przewodów elektrycznych, badania wytrzymałości na rozciąganie czy próby wytrzymałościowe, odgrywają istotną rolę w zapewnieniu niezawodności i trwałości wiązek kablowych.
Kluczowe aspekty końcowej kontroli jakości wiązki elektrycznej
Końcowa kontrola jakości gotowej wiązki elektrycznej skupia się na dokładnym i skrupulatnym sprawdzeniu każdego detalu, aby upewnić się, że produkt spełnia najwyższe standardy jakości i jest zgodny z wymaganiami specyfikacji technicznych. Mówimy tu w kontekście zapewnienia nie tylko doskonałej jakości, ale także bezpieczeństwa i zaufania klientów do dostarczanych produktów.
Jak sprawdzamy gotową wiązkę kablową?
- Wizualna inspekcja Wizualna inspekcja jest niezwykle istotnym aspektem końcowej kontroli jakości. Przeszkolony personel dokładnie sprawdza każdą wiązkę elektryczną pod kątem wyglądu, jakości zaciskania konektorów, izolacji przewodów oraz poprawności etykietowania. Wszelkie wady, takie jak niesymetryczne zaciskanie czy nieprawidłowo umieszczone etykiety, są identyfikowane i rejestrowane.
- Testy wytrzymałościowe i funkcjonalne – pomiar siły zrywu W trakcie końcowej kontroli jakości wiązki elektrycznej niezastąpionym narzędziem jest tester przewodów elektrycznych, którego głównym celem jest przeprowadzenie zarówno testów wytrzymałościowych – takich jak pomiar siły zrywania( Tabela 1 – pomiar siły zrywania ), jak i funkcjonalnych. Oprócz badań potencjalnych przerw w obwodach, wiązki kablowe podlegają rygorystycznym testom obciążeniowym prądu i napięcia, by zweryfikować ich zdolność do utrzymania odpowiednich parametrów. Ważnym aspektem jest również wykonywanie testów funkcjonalnych, które pozwalają upewnić się, że wiązka elektryczna działa zgodnie z projektem. Proces testowania wiązek kablowych obejmuje zarówno badanie wytrzymałości na rozciąganie, jak i próby wytrzymałościowe pod kątem ciągłości przewodów. W ramach tych procedur zastosowanie znajduje miernik siły zrywania końcówek kablowych, który dokładnie określa, czy wiązka elektryczna jest odporna na działania związane z jej użytkowaniem. Tester przewodów elektrycznych odgrywa kluczową rolę w procesie kontroli jakości wiązek kablowych, umożliwiając dokładne badania funkcjonalności, wytrzymałości oraz integralności przewodów.
- Sprawdzenie izolacji Izolacja przewodów w wiązce elektrycznej jest kluczowym aspektem zapewnienia bezpieczeństwa i niezawodności produktu. Podczas kontroli jakości sprawdzane jest, czy izolacja jest odpowiednio wykonana i czy spełnia określone normy bezpieczeństwa.
- Identyfikacja i etykietowanie W tym etapie kontrola jest również skoncentrowana na poprawnym oznaczeniu i identyfikacji przewodów oraz konektorów w wiązce. Zapewnienie odpowiednich etykiet i identyfikatorów ułatwia instalację i obsługę wiązki elektrycznej.
- Rejestracja i dokumentacja Wszystkie wyniki kontroli jakości są starannie dokumentowane i rejestrowane. Rejestracja pozwala na śledzenie wyników i identyfikację ewentualnych problemów, a także jest istotna dla celów audytu i kontroli jakości.
- Bezpieczeństwo Kluczowym aspektem końcowej kontroli jakości jest zapewnienie bezpieczeństwa użytkowania wiązki elektrycznej. Wiązki elektryczne są powszechnie używane w różnych aplikacjach, w tym w pojazdach, maszynach i urządzeniach medycznych, dlatego niezawodność i jakość są niezbędne dla bezpiecznej pracy tych urządzeń.
Tabela 1.
Przekrój przewodu | Siła zrywu | |
---|---|---|
mm2 | AWGa | N |
0,05 | 30 | 6 |
0,08 | 28 | 11 |
0,12 | 26 | 15 |
0,14 | 18 | |
0,22 | 24 | 28 |
0,25 | 32 | |
0,32 | 22 | 40 |
0,5 | 20 | 60 |
0,75 | 85 | |
0,82 | 18 | 90 |
1,0 | 108 | |
1,3 | 16 | 135 |
1,5 | 150 | |
2,1 | 14 | 200 |
2,5 | 230 | |
3,3 | 12 | 275 |
4,0 | 310 | |
5,3 | 10 | 355 |
6,0 | 360 | |
8,4 | 8 | 370 |
10,0 | 380 | |
Testowanie połączenia zaciskanego terminali/konektorów na wiązce elektrycznej według IEC 60760, klauzula 17 i IEC 61210. |
Najważniejsze kryteria jakości przy produkcji wiązek elektrycznych
- Bezpieczeństwo: ważne jest, aby wiązka elektryczna była bezpieczna dla użytkownika i nie stanowiła zagrożenia dla jego zdrowia i życia.
- Trwałość: wiązka elektryczna powinna być trwała i odporna na uszkodzenia mechaniczne oraz zakłócenia elektryczne.
- Wytrzymałość mechaniczna: każda wiązka kablowa powinna spełniać wymogi norm dotyczących siły zrywu.
- Dokładność połączeń: połączenia między przewodami powinny być dokładne i trwałe, aby zapewnić prawidłowy przepływ prądu.
- Izolacja: izolacja wiązki elektrycznej powinna być skuteczna w ochronie przed uszkodzeniami i zakłóceniami elektrycznymi.
- Dokładność długości przewodów: długości przewodów powinny być dokładne i odpowiednie dla potrzeb klienta.
- Wydajność: wiązka elektryczna powinna działać zgodnie z projektem i specyfikacją techniczną.
- Testowanie: ważne jest, aby wiązka elektryczna była testowana przed wysyłką, aby upewnić się, że spełnia ona wymagania jakościowe.
- Zgodność z normami: ważne jest, aby wiązka elektryczna była zgodna z obowiązującymi normami i przepisami.
- Estetyka: ważne jest, aby wiązka elektryczna była estetyczna i zgodna z oczekiwaniami klienta.
- Pakowanie: ważne jest, aby wiązka elektryczna była odpowiednio zabezpieczona przed transportem i przechowywaniem.
Przygotowanie wiązek elektrycznych do transportu
Po wytworzeniu wiązek elektrycznych dbamy także o to, aby były one odpowiednio zabezpieczone i zapakowane do wysyłki i transportu do klienta. Często stosujemy dedykowane opakowania , które sprawiają, że wiązka kablowa prezentuje się estetycznie oraz jej wrażliwe elementy są chronione. Zgodnie z życzeniem klienta segregujemy wiązki oraz jasno je oznaczamy, tak, aby ułatwić późniejszy ich montaż w maszynie docelowej. Przy pakowaniu kierujemy się solidnością. Gotowe produkty umieszczane są w pudełku kartonowym, zabezpieczane folią stretch, tak aby chronić wiązki przed wilgocią, a puste przestrzenie wypełniane są pianką, co sprawia, że nawet najbardziej delikatne produkty docierają do klienta nienaruszone. Często stosujemy różnorodne formy etykiet, które pozwalają z łatwością identyfikować produkt.
Gametop
19 sierpnia 2022Dzięki za solidny wpis. Projektowanie urządzeń zawierających wiązki elektryczne nie jest łatwą czynnością. Jest sporo czynników które należy wziąć pod uwagę. Wiązki kablowe powinny być wykonywane według ścisłych wytycznych, zarówno technicznych i jakościowych.